If an analog Input shows a precision problem or an offset on the real measure. we can put a correction by the IEC application when the measurement error is clearly identified.
To identify the measurement error, you need to have a temperature references or a calibrated thermometer, in order to compare with the read value on the temperature input of the TM3 module.
Because unfortunately, we haven't possibility to calibrate the temperature module, this step is make in factory with a tolerance of 0.1% of the totality of measurement scale.
Example : Thermocouple K
The scale is 1500°C (-200°C to 1300°C), the error on the real measure can up to 15°C.
Temperature input configuration:
- %IW1.0 configured with thermocouple K (scale: -200°C to 1300°C)
- Measurement error => 7.5°C (compared to a calibrated thermometer)
Correction by program (IEC application):
-For a linear error => Temp_corrected := %IW1.0 + (%IW1.0*0.0005) ; // 0.0005 = 7.5/1500 => (correction coefficient = error / scale)
-For a constant error => Temp_corrected := %IW1.0+75 ;
Example : PT100
The scale is 1050°C (-200°C to 850°C), the error on the real measure can up to 10.5°C.
Temperature input configuration:
- %IW1.1 configured with PT100 (scale: -200°C to 850°C)
- Measurement error => 5°C (compared to a calibrated thermometer)
Correction by program (IEC application):
-For a linear error => Temp_corrected := %IW1.1 + (%IW1.1*0.000476) ; // 0.000476 = 5/1050 => (correction coefficient = error / scale)
-For a constant error => Temp_corrected := %IW1.1+50 ;
To identify the measurement error, you need to have a temperature references or a calibrated thermometer, in order to compare with the read value on the temperature input of the TM3 module.
Because unfortunately, we haven't possibility to calibrate the temperature module, this step is make in factory with a tolerance of 0.1% of the totality of measurement scale.
Example : Thermocouple K
The scale is 1500°C (-200°C to 1300°C), the error on the real measure can up to 15°C.
Temperature input configuration:
- %IW1.0 configured with thermocouple K (scale: -200°C to 1300°C)
- Measurement error => 7.5°C (compared to a calibrated thermometer)
Correction by program (IEC application):
-For a linear error => Temp_corrected := %IW1.0 + (%IW1.0*0.0005) ; // 0.0005 = 7.5/1500 => (correction coefficient = error / scale)
-For a constant error => Temp_corrected := %IW1.0+75 ;
Example : PT100
The scale is 1050°C (-200°C to 850°C), the error on the real measure can up to 10.5°C.
Temperature input configuration:
- %IW1.1 configured with PT100 (scale: -200°C to 850°C)
- Measurement error => 5°C (compared to a calibrated thermometer)
Correction by program (IEC application):
-For a linear error => Temp_corrected := %IW1.1 + (%IW1.1*0.000476) ; // 0.000476 = 5/1050 => (correction coefficient = error / scale)
-For a constant error => Temp_corrected := %IW1.1+50 ;
Released for:Schneider Electric United Arab Emirates
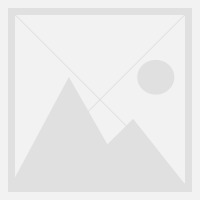
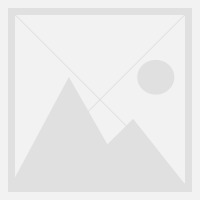