How can we help you today?
Is it possible to install a contactor downstream from a variable speed drive?
It is possible to install a contactor downstream of a variable speed drive but this involves a high risk of damage to the equipment if the contactor is actuated when the drive is powering the motor.
To reduce this risk, ATV61 and ATV71 drives incorporate a configurable function which allows the drive to control the contactor directly.
ATV31 and ATV312 drives do not have such a sophisticated function, but they do have a setting for reducing the effect of destructive over voltages caused by the failure of a contactor.
CAUTION: On the ATV11 and ATV12 drives there is no provision at all for this operation so on these drive we strongly advise against you installing a down stream contactor
ATV61 and ATV71
Control of a downstream contactor by an ATV61 or ATV71 drive means that it is the drive, and the drive alone, which controls the opening and closing of a contactor connected between the drive and the motor. This is to prevent damage to the drive's power bridge, which can occur if the downstream contactor opens when the drive is powering the motor.
Description of operation
When a run signal is sent to the drive (normally onto LI1 for run forward or LI2 for run reverse), this operates either a logic output or a relay output (LO1 to LO4 or R2 to R4). This brings in the down stream contactor by applying current to the coil of KM2 via K20. When the STOP request is sent to the drive, the drive monitors the current in the motor and only deactivates the contactor’s coil when this value is zero which drops out the contactor KM2. To monitor the state of the contactor a normally closed contact from KM2 is connected to one of the drives digital inputs LIx. If a problem occurs with the contactor the drive will trip and display FCF2 the contactor fails to close or FCF1 if the contactor fails to open
Settings
To set up your ATV61 / 71 drive to achieve the above operation you must follow the procedure below.
From the DRIVE MENU select 1.7 APPLICATION FUNCT.
Then scroll down to OUTPUT CONTACTOR CMD and enter
The first thing is to select the output of the drive to control the the contactor. This is done in the following manner
In OUT Contactor ass. (OCC)
You select either LO1 to LO4 or R2 to R4
The next thing is to set up the feed back monitoring the state of the contactor so in Output contact.fdbk (rCA)
At this point you select the feedback input LI2 to LI6
The motor will start when this input changes from 1 to 0
The next setting is the time delay for the motor to RUN
Time to motor run (dbS) - this is the time delay between the signal onto LI1 or LI2 (run fwd or rev) and the sending of the motor run command. This time delay must be set to more than time take for the output contactor to close.
The final setting is the time after which the motor should be stopped and it is safe for the output contactor to open
Time to open contactor (dAS)
This should be set to the time which is greater than the time it takes the contactor to open
Example of ATV71 / 61 wiring
The same functionality can now be found in the ATV320 , ATV340 ,ATV600 and ATV900 series drives which replace the ATV61/71 drives.
ATV31 / ATV312
If you have to use a contactor downstream of either an ATV31 or ATV312 you must make sure that your control circuit ensures that the contactor is in before the motor start signal is applied, and the motor is stopped before the contactor is out. Unlike the bigger drives the ATV31 and ATV312 can not directly control the contactor down stream. But by using the following setting you can give the drive a little protection.
In FLt- Menu (Fault Menu)
Set OPL (Output Phase Lose) to OAC. This does not trip the drive on output phase lose but manages the output voltage to avoid a damaging over current and will perform a Catch on the Fly if the supply is re-established
If you do an Auto Tune on this set up and it fails check the downstream contactor is closed and try again.
Released for:Schneider Electric Australia
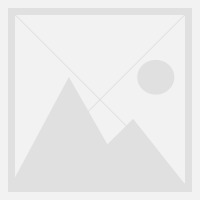
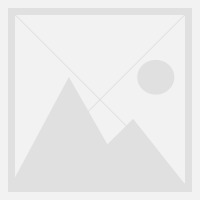
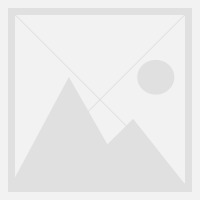
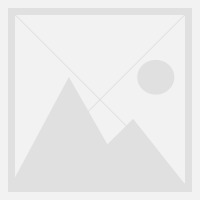
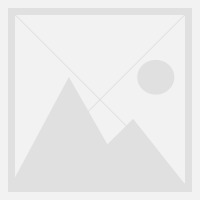
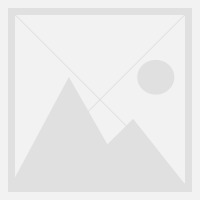
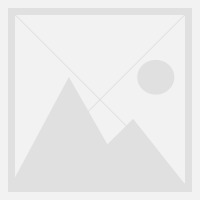
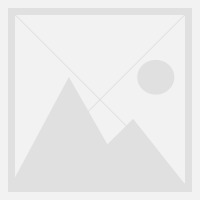
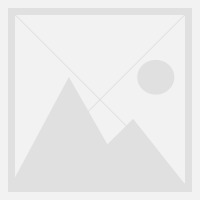
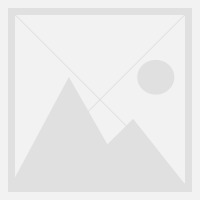