When TesyT is configured to 2-step operating mode (2-step 2wire or 2-step 3wire), this operating mode can be used for
Please note that if TesysT is connected inside motor delta (wiring diagram shown in the manual) and you use 2-step operating mode you have to enable “motor star-delta”

With this setting, the current flown via current transformer is sqrt(3) times lower in step 2 (delta), but TEsyst will recalculate and show always line current.
So FLC current must be set to line current (not for the current inside motor delta), this value can be copied from motor plate for delta connection
Thermal protection will consider starting phase with the line current = current via CT and running phase with line current = 1.73 * current via CT.
If you start your motor using starting reactor or autotransformer, or if you use star-delta start but TesysT is connected in line circuit (not inside motor delta), the motor star-delta parameter must be disabled. The line current is always equal to current via CT.
Switching from step 1 to step 2 is done according to conditions set in threshold and timeout

In my configuration, switching from star to delta is done if motor current goes below 145%FLC (of course at the beginning of starting the current must go above 145%FLC) or after 5 seconds since start command, whichever condition is fulfilled earlier. 1second is interlock between star-delta switching.
To sum up, in start-delta start, always set FLC current to the value shown on motor plate for delta connection, which is steady current during motor running.
If supply network is 400V, 50Hz the motor plate should look like :
Y / D
690V/ 400V
17A / 30A (example)
FLC to be set to 30A
- Star-delta start or
- Starting using starting reactors or
- Starting using autotransformer
Please note that if TesysT is connected inside motor delta (wiring diagram shown in the manual) and you use 2-step operating mode you have to enable “motor star-delta”
With this setting, the current flown via current transformer is sqrt(3) times lower in step 2 (delta), but TEsyst will recalculate and show always line current.
So FLC current must be set to line current (not for the current inside motor delta), this value can be copied from motor plate for delta connection
Thermal protection will consider starting phase with the line current = current via CT and running phase with line current = 1.73 * current via CT.
If you start your motor using starting reactor or autotransformer, or if you use star-delta start but TesysT is connected in line circuit (not inside motor delta), the motor star-delta parameter must be disabled. The line current is always equal to current via CT.
Switching from step 1 to step 2 is done according to conditions set in threshold and timeout
In my configuration, switching from star to delta is done if motor current goes below 145%FLC (of course at the beginning of starting the current must go above 145%FLC) or after 5 seconds since start command, whichever condition is fulfilled earlier. 1second is interlock between star-delta switching.
To sum up, in start-delta start, always set FLC current to the value shown on motor plate for delta connection, which is steady current during motor running.
If supply network is 400V, 50Hz the motor plate should look like :
Y / D
690V/ 400V
17A / 30A (example)
FLC to be set to 30A
Released for:Schneider Electric Australia
When TesyT is configured to 2-step operating mode (2-step 2wire or 2-step 3wire), this operating mode can be used for
Please note that if TesysT is connected inside motor delta (wiring diagram shown in the manual) and you use 2-step operating mode you have to enable “motor star-delta”

With this setting, the current flown via current transformer is sqrt(3) times lower in step 2 (delta), but TEsyst will recalculate and show always line current.
So FLC current must be set to line current (not for the current inside motor delta), this value can be copied from motor plate for delta connection
Thermal protection will consider starting phase with the line current = current via CT and running phase with line current = 1.73 * current via CT.
If you start your motor using starting reactor or autotransformer, or if you use star-delta start but TesysT is connected in line circuit (not inside motor delta), the motor star-delta parameter must be disabled. The line current is always equal to current via CT.
Switching from step 1 to step 2 is done according to conditions set in threshold and timeout

In my configuration, switching from star to delta is done if motor current goes below 145%FLC (of course at the beginning of starting the current must go above 145%FLC) or after 5 seconds since start command, whichever condition is fulfilled earlier. 1second is interlock between star-delta switching.
To sum up, in start-delta start, always set FLC current to the value shown on motor plate for delta connection, which is steady current during motor running.
If supply network is 400V, 50Hz the motor plate should look like :
Y / D
690V/ 400V
17A / 30A (example)
FLC to be set to 30A
- Star-delta start or
- Starting using starting reactors or
- Starting using autotransformer
Please note that if TesysT is connected inside motor delta (wiring diagram shown in the manual) and you use 2-step operating mode you have to enable “motor star-delta”
With this setting, the current flown via current transformer is sqrt(3) times lower in step 2 (delta), but TEsyst will recalculate and show always line current.
So FLC current must be set to line current (not for the current inside motor delta), this value can be copied from motor plate for delta connection
Thermal protection will consider starting phase with the line current = current via CT and running phase with line current = 1.73 * current via CT.
If you start your motor using starting reactor or autotransformer, or if you use star-delta start but TesysT is connected in line circuit (not inside motor delta), the motor star-delta parameter must be disabled. The line current is always equal to current via CT.
Switching from step 1 to step 2 is done according to conditions set in threshold and timeout
In my configuration, switching from star to delta is done if motor current goes below 145%FLC (of course at the beginning of starting the current must go above 145%FLC) or after 5 seconds since start command, whichever condition is fulfilled earlier. 1second is interlock between star-delta switching.
To sum up, in start-delta start, always set FLC current to the value shown on motor plate for delta connection, which is steady current during motor running.
If supply network is 400V, 50Hz the motor plate should look like :
Y / D
690V/ 400V
17A / 30A (example)
FLC to be set to 30A
Released for:Schneider Electric Australia
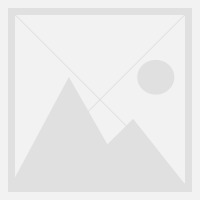
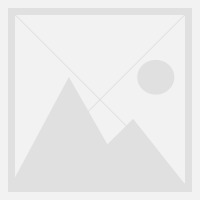
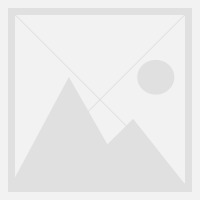
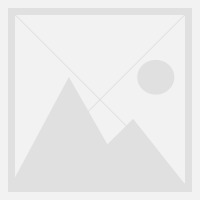
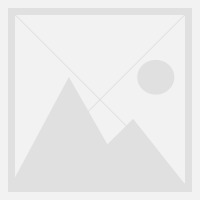
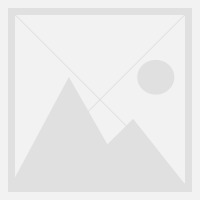
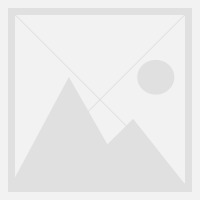
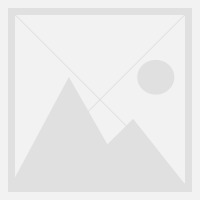
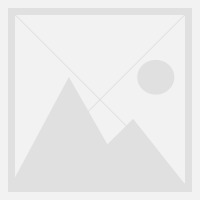
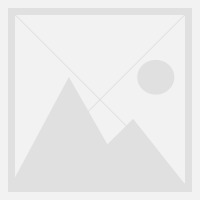
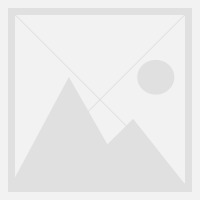
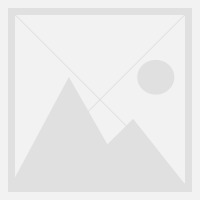
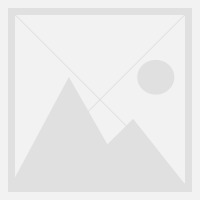
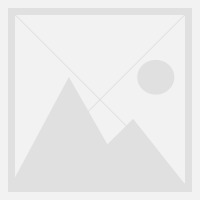
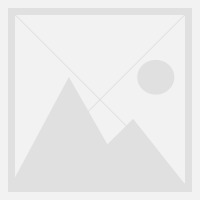
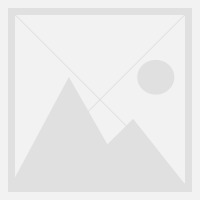
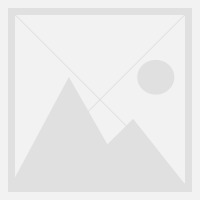
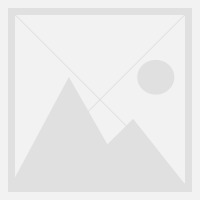
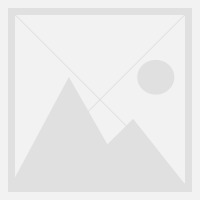
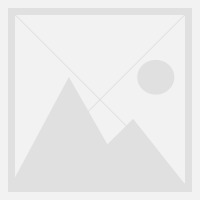