Although the programming manual does not describe this combination, the required function is possible to manage.
It is obvious that the PID regulator works with channel 1 only (FR1). Channel 2 (FR2) is always without PID. Therefore PID auto /manual cannot switch control to channel2.
And channel 2 is needed for +/- speed because this function works only on channel 2.
Section 8.1 on page 169 of ATV600 programming manual_version 08 shows more hints regarding priority PID auto manual and channel switching. If channel 2 (FR2) is selected, it overrides PID. It means that whatever appears on PID output, it is still on channel1. And if we switch to channel 2, then the value on channel 1 is ignored. It is even not necessary to configure pID auto/manual
Attached example with the configuration.
In the configuration, it was used:
Type of PID control = N/A. Can be modified by the customer. It will affect the unit of PID reference and feedback
Feedback on AI3 (Voltage 0-10V). No problem to change it to AI2 or use the current signal according to the customer's preferences
Scaling for feedback and reference as well as proportional and integral gain - is up to the customer
Auto/manual not configured
FR1=embedded eth (for this particular request)
FR2=freq ref via DI
CHCF (channel switching)=DI6. The customer can assign the input that he needs.
Up speed input = DI3. Free to choose other input
Down speed input = DI5. Free to choose other input
STR (ref freq save) = Save to RAM. Free to be changed by the customer. It affects the last reference value (cleared or retained) after stopping or powering off the drive.
When controlling over ethernet, it is necessary to write into 2 registers:
8501 (command register). In CIA402 mode (default) sequence of value 6-->7-->15 gives start
8503 (PISP register). Here you have to write value of PID setpoint.
Text in bold means that it must be configured and used.
Text in italic means its configuration is up to customer
In my example if DI6=0, PID is active and commands + PID setpoint comes from ethernet (register 8501, 8503)
If DI6=1, ATV is awaiting run command via terminals (DI1) and reference is by +/- speed using DI3 and DI5. I used "STR="Save to RAM", but it has to be configured according to customer preferences.
If it is required to switch from auto to manual during motor running and to avoid motor stop (DI1 must remain high) , it can be nice to keep TCC=2-wire control and TCT=Level.
Released for:Schneider Electric Canada
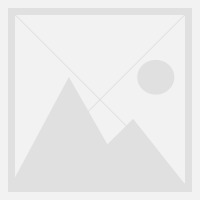
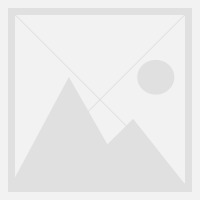
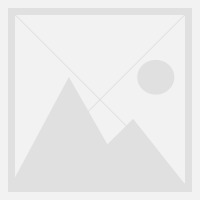
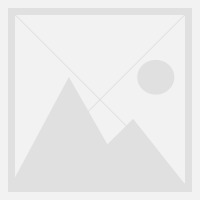