These comments apply to all contactor applications but specifically mention lighting because of the long periods of energisation often experienced.
There is no "lifespan" for Schneider Electric contactor coils and they are designed to be able to cope with continuous duty. Where one specific site is experiencing repeated coil failure, it is almost always a result of conditions of use, e.g.:
- Overvoltage
- Over temperature (ambient)
- Physical obstruction preventing the contactor closing fully
- Undervoltage where the coil is not producing sufficient force to keep the contactor armature fully sealed
Lighting contactors are often energised for very long periods, sometimes weeks or months continuously, therefore it is very important to ensure that ambient temperatures in enclosures are maintained within specified levels.
For TeSys Deca contactors, the recommended maximum is 60°C. This is air temperature immediately around the contactor, not the overall temperature of the enclosure, so watch out for hot spots. Even in panels and enclosures that do not appear to be overheating it may be necessary to fit circulation fans to ensure even distribution of the cooler air.
A minor increase is normally permissible as long as the nominal coil voltage is not exceeded. A minor voltage increase (1.1 * nominal) is permissible if the recommended temperature is not exceeded but a prolonged increase in both, even minor, can cause failure.
Below is an example image of a Thermal Picture of the inside of a control panel.
For TeSys Deca contactors, the recommended maximum is 60°C. This is air temperature immediately around the contactor, not the overall temperature of the enclosure, so watch out for hot spots. Even in panels and enclosures that do not appear to be overheating it may be necessary to fit circulation fans to ensure even distribution of the cooler air.
A minor increase is normally permissible as long as the nominal coil voltage is not exceeded. A minor voltage increase (1.1 * nominal) is permissible if the recommended temperature is not exceeded but a prolonged increase in both, even minor, can cause failure.
Below is an example image of a Thermal Picture of the inside of a control panel.
By far the most common cause of contactor coil failure is undervoltage. There may be sufficient voltage to pull the contactor in, but not enough to keep the coil armature firmly "sealed". This will result in overcurrent in the coil as the full impedance of the coil is not achieved until the mating faces are perfectly closed.
This can also happen in dusty environments were contamination can build up between the mating surfaces. Even a voltage which is so low as to prevent the contactor pulling in at all can burn out a coil as until the contactor pulls in there is very little impedance to coil and the coil may be carrying many times the intended current.
This can also happen in dusty environments were contamination can build up between the mating surfaces. Even a voltage which is so low as to prevent the contactor pulling in at all can burn out a coil as until the contactor pulls in there is very little impedance to coil and the coil may be carrying many times the intended current.
In some cases failure is a result of a combination of these factors.
These comments apply to AC coils, DC coils have not been mentioned as they are very different and not normally used in lighting applications. Because of available voltages in common lighting applications most lighting contactors will have 230 or 240 volt AC coils.
Which brings us to a final point. Unless locally transformed , there is no 230V supply. In UK it is still 240VAC and 220VAC in mainland Europe and Republic of Ireland. A 230V coil is designed to run on both, but it will be 220V at the bottom end of its range and 240V at the top. A 240V coil is specifically designed for UK voltage systems.
For lighting applications of long duration we would always recommend using a 240V coil in the UK as it is optimised for the 240V supply and less likely to be effected by fluctuations in UK supplies than a 230V coil which is already running nearer the top of its range. In theory it should make no difference as 230V coils are designed for both, but in a situation which is known to be "difficult" it pays to eliminate as many potential issues as possible.
Which brings us to a final point. Unless locally transformed , there is no 230V supply. In UK it is still 240VAC and 220VAC in mainland Europe and Republic of Ireland. A 230V coil is designed to run on both, but it will be 220V at the bottom end of its range and 240V at the top. A 240V coil is specifically designed for UK voltage systems.
For lighting applications of long duration we would always recommend using a 240V coil in the UK as it is optimised for the 240V supply and less likely to be effected by fluctuations in UK supplies than a 230V coil which is already running nearer the top of its range. In theory it should make no difference as 230V coils are designed for both, but in a situation which is known to be "difficult" it pays to eliminate as many potential issues as possible.
Released for:Schneider Electric Ireland
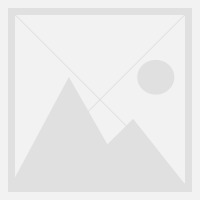
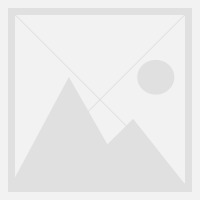
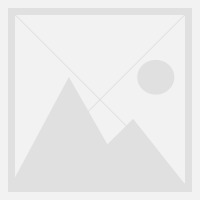
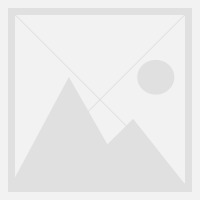
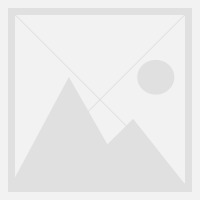
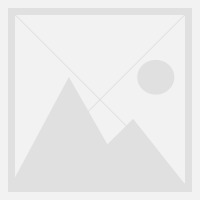
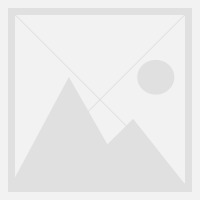
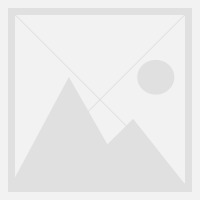
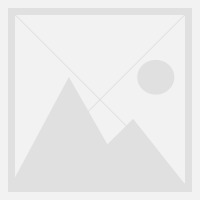
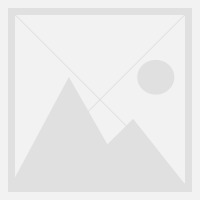