General principle
A PID controller is used to correct the deviation between the reference and the measurement feedback within an acceptable period. It does so by increasing or decreasing the process output, by means of 3 main parameters called gains (proportional gain, integral gain and derivative gain), which can accelerate, delay and stabilize this correction.
The PID control function can be shown as a black box represented by a comparator with 2 inputs (reference and feedback). The result of this comparator controls the process output.
The term "acceptable" means that the correction must be made more or less quickly according to the type of process. For example, temperature control does not usually require very fast reactions: The time constants for industrial furnaces may sometimes be several hours.
Conversely, position control is a process requiring very fast reactions (ms).
The reference is the target value for the physical unit to be obtained at the output (temperature, pressure, movement, etc.)
The measurement feedback is used to check the deviation between the state of the process and the reference.
This PID control function is available in the form of:
Application-specific function in ATV variable speed drives (ATV12, ATV21, ATV212 , ATV32 ,ATV312,ATV320, ATV340, ATV61, ATV71 and ATV600 and 900 series).
Separate dedicated controller (REG24, REG48 and REG96 temperature controller)
Function blocks in Premium, M340 and Twido, M221, M241, M580
The remainder of the documentation will describe this PID function applied to variable speed drives.
Reference
The reference is the value written by the user. There are 4 types:
Internal reference: This is written in a dedicated parameter that can only be accessed via the integrated display terminal, and can therefore only be modified by a trained user.
This type of reference is mainly used when a fixed reference is required.
External reference by potentiometer: The reference is provided by an external potentiometer, and can therefore be modified by the user at any time. The power supply to the potentiometer (0-10 V) is provided by the drive itself.
External reference by means of preset speeds: The reference will be provided by switching logic inputs which are available on all drives. Each state of the inputs can be associated with a single reference.
The advantage is having several set references that are very easy to access for example using a mechanical switch (except for ATV12 and ATV312).
External reference by means of analog input (0-10 V or 0-20 mA or 4-20 mA): Any device generating an analog signal can provide the drive with a reference: Zelio, Twido, M340, M580 Premium and other PLCs, XBT , HMI units, and Analog output sensors.
Measurement feedback
The measurement feedback is the analog signal from the sensor. There are 2 types:
Voltage analog value (0-10 V)
Current analog value (0-20 mA or 4-20 mA)
On some drives it is possible to set the input scale to adapt to the sensor.
Example: To measure a maximum pressure of 7 bar, you need to find the nearest sensor to this measurement range, hence a 0-10 bar/0-10 V sensor. There will therefore be 3 volts not used for the measurement feedback, the measurement feedback will never be full scale and it will lose resolution. ATV61 and ATV71 drives can calibrate the voltage analog input from 0-10 V to 0-7 V.
PID controller
This attempts to reduce the deviation between the measurement feedback and the reference by increasing or decreasing the process output.
If the measurement feedback value is greater than the reference value, the deviation is positive and the ATV drive's PID controller will decelerate the motor.
Conversely, if the measurement feedback value is less than the reference value, the deviation is negative and the ATV drive's PID controller will accelerate the motor.
Caution: In some cases, the PID must be reversed: positive deviation => motor acceleration (for example, temperature control). To carry out this reversal on an ATV212, see the following link: PID reversal on ATV212
The system response time can be adjusted by means of the 3 gain parameters.
Caution: The factory settings of ATV drives generate response times that are compatible with most pressure and temperature processes, but adjustment is still possible if there are instabilities.
A PID controller is used to correct the deviation between the reference and the measurement feedback within an acceptable period. It does so by increasing or decreasing the process output, by means of 3 main parameters called gains (proportional gain, integral gain and derivative gain), which can accelerate, delay and stabilize this correction.
The PID control function can be shown as a black box represented by a comparator with 2 inputs (reference and feedback). The result of this comparator controls the process output.
The term "acceptable" means that the correction must be made more or less quickly according to the type of process. For example, temperature control does not usually require very fast reactions: The time constants for industrial furnaces may sometimes be several hours.
Conversely, position control is a process requiring very fast reactions (ms).
The reference is the target value for the physical unit to be obtained at the output (temperature, pressure, movement, etc.)
The measurement feedback is used to check the deviation between the state of the process and the reference.
This PID control function is available in the form of:
Application-specific function in ATV variable speed drives (ATV12, ATV21, ATV212 , ATV32 ,ATV312,ATV320, ATV340, ATV61, ATV71 and ATV600 and 900 series).
Separate dedicated controller (REG24, REG48 and REG96 temperature controller)
Function blocks in Premium, M340 and Twido, M221, M241, M580
The remainder of the documentation will describe this PID function applied to variable speed drives.
Reference
The reference is the value written by the user. There are 4 types:
Internal reference: This is written in a dedicated parameter that can only be accessed via the integrated display terminal, and can therefore only be modified by a trained user.
This type of reference is mainly used when a fixed reference is required.
External reference by potentiometer: The reference is provided by an external potentiometer, and can therefore be modified by the user at any time. The power supply to the potentiometer (0-10 V) is provided by the drive itself.
External reference by means of preset speeds: The reference will be provided by switching logic inputs which are available on all drives. Each state of the inputs can be associated with a single reference.
The advantage is having several set references that are very easy to access for example using a mechanical switch (except for ATV12 and ATV312).
External reference by means of analog input (0-10 V or 0-20 mA or 4-20 mA): Any device generating an analog signal can provide the drive with a reference: Zelio, Twido, M340, M580 Premium and other PLCs, XBT , HMI units, and Analog output sensors.
Measurement feedback
The measurement feedback is the analog signal from the sensor. There are 2 types:
Voltage analog value (0-10 V)
Current analog value (0-20 mA or 4-20 mA)
On some drives it is possible to set the input scale to adapt to the sensor.
Example: To measure a maximum pressure of 7 bar, you need to find the nearest sensor to this measurement range, hence a 0-10 bar/0-10 V sensor. There will therefore be 3 volts not used for the measurement feedback, the measurement feedback will never be full scale and it will lose resolution. ATV61 and ATV71 drives can calibrate the voltage analog input from 0-10 V to 0-7 V.
PID controller
This attempts to reduce the deviation between the measurement feedback and the reference by increasing or decreasing the process output.
If the measurement feedback value is greater than the reference value, the deviation is positive and the ATV drive's PID controller will decelerate the motor.
Conversely, if the measurement feedback value is less than the reference value, the deviation is negative and the ATV drive's PID controller will accelerate the motor.
Caution: In some cases, the PID must be reversed: positive deviation => motor acceleration (for example, temperature control). To carry out this reversal on an ATV212, see the following link: PID reversal on ATV212
The system response time can be adjusted by means of the 3 gain parameters.
Caution: The factory settings of ATV drives generate response times that are compatible with most pressure and temperature processes, but adjustment is still possible if there are instabilities.
Released for:Schneider Electric India
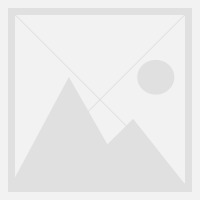
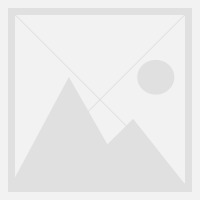
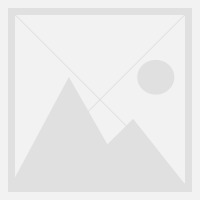
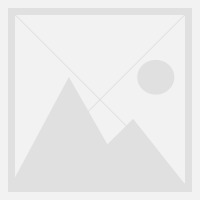
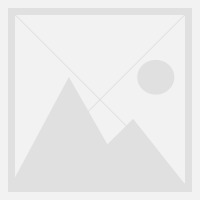
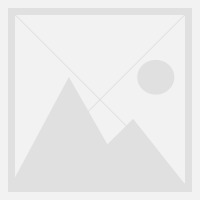
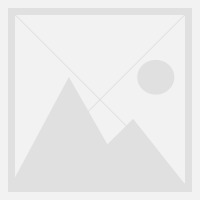
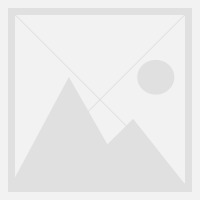
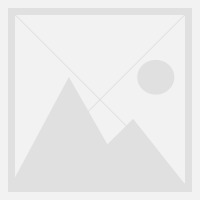
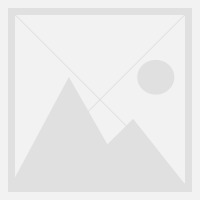