Search FAQs
Can I control a motor with a rating lower than that of the variable speed drive?
Yes it is possible to use a motor with a lower rating than that of the drive.
For instance If you are trying to test a system with either a very small motor or no motor connected you may get OPF (phase loss detection issues).
On the drive we can set down the normal running current down to 25% of the drive rating. The DRC current setting is 25% to 1.50% of drive rating.
However running a very small motor on a drive may give instability in the running of the motor, where you may have to alter gain parameters for better stability. Also if the small motor is not loaded then you may see issues where the output phase loss can be triggered if not enough current flow to the motor is seen. So it is best to use a drive down to the 50% or rating to avoid these possible issues.
Example for an ATV31HD11N4:
If the nominal current for a ATV31HD11N4 is 27.7 A corresponding to an 11 kW motor, you can configure the current parameters as follows:
nCr: Motor current as read on the rating plate, configurable down to 25% of the drive nominal current, i.e. 7 A for a 4 kW motor
Ith: Thermal protection can be set down to 20%
CLI: Current limit can be set down to 25%
This characteristic can useful in terms of stocking replacement drives. A variable speed drive can replace 3 to 4 sizes of drive until the drive that has failed has been repaired. But the setting process may prove difficult because of stability issues.(see the next paragraph).
Continuous use in industry
For an industrial application, the motor power should not be less than 50% of the drive nominal power in order to maintain the nominal performance. For example, in the case of the ATV31HD11N4 drive, do not use a motor with a power rating below 7.5 kW
Below this value, there is a risk of unstable operation and the gains will have to be adjusted.
For laboratory applications, the rating can be decreased a little further. The limit depends on the resolution of the current sensors, which may become insufficient to ensure correct speed and torque control.
Whatever the case, it is necessary to enter both the motor parameters and the protection parameters correctly. (Do not forget to perform an auto-tuning)
Testing of correct drive operation with very small motor or no motor
Acceptance testing of installations or pre-delivery to site testing, often involves testing for correct drive operation . For high ratings, testing the drive with its very bulky and very heavy motor is totally impractical. So for each range of drives, it must be possible to test it with a motor of a very low rating, or no motor at all.
To test on very small or no motor set the parameters as shown in the following lists:
ATV31 and ATV312
Deactivate the motor phase loss: FLt menu => OPL=no
Configure the voltage/frequency ratio: drC menu => UFt = L
ATV320
Deactivate the motor phase loss: FLt menu => OPL- > OPL =no
Motor control is VF/2 pt as STD and does not need to be changed from default.
ATV71
1.8 FAULT MANAGEMENT menu => Motor phase loss = nO
1.4 MOTOR CONTROL menu => Motor control type = U/F 2pts or U/F 5pts
ATV21 and ATV212
Deactivate F605: F605 =0
Pt = 0 V/Hz motor control mode
Please note that as you may be testing on a very small motor compared to the power rating of the drive you may see instability of the operation due to how the gains are set in the drive as the factory default settings.
ATV600 and 900 series.
Menu, complete settings => error warning and handling => output phase loss=> function inactive.
Again on a small motor test it may be instability in the motor speed so, because of the motor control law set as default, it may be necessary to alter the control law to v/f 2 point for testing purposes.
Released for:Schneider Electric UK
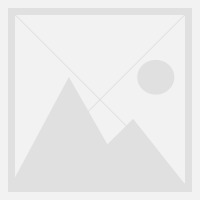
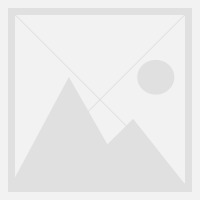
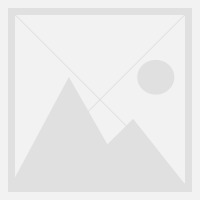
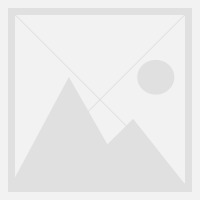
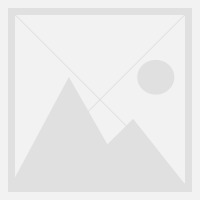
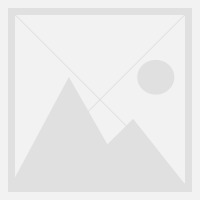
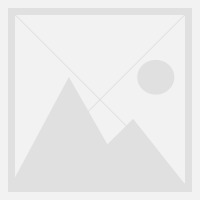
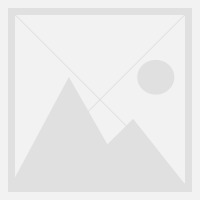
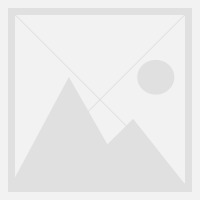
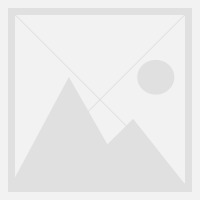