Prerequisite:
List of the required files:
It is recommended to start operation with device having default setting. Part of the configuration process is to recall bay type definition. This process fails if device would have assigned some I/O elements required by selected bay type. For example bay type = 2 needs UA01 (which is the U601 for 40TE case and U1201 for 84TE case):
If U901 (U1201) input is already assigned to any protection signal, the bay type setting would be rejected.
Above example would result with rejection of any BTC definition if being configured prior to bay type selection.
The rejection of the bay type assignment can be result of several configuration elements being present, thus instead of individual identification of all locking parameters it is recommended to start the setting procedure either with clean device – just after unpacking from factory package or to make it empty by means of cold restart.
Whole configuration process can be split into several parts, as follows:
Upload .hex file to the device - please follow procedure from the document "TQ_PAST-2014-BW-03-c (ES1S for BTC download for P139[P439].65x)"
b. Type of bay
Open setting file and send the bay type number:
This parameter can’t be transferred as an group, it needs to be send as single entry from the context menu as depicted above.
c. SIG_1 elements (if configured)
If SIG_1 elements are configured, it is recommended to send them at the beginning of the setting procedure as for some firmware versions, the setting tool sends them in wrong order – first trying to configure elements using SIG_1 and then to add SIG_1 itself to configuration. This would fail as element should be active before it could be used.
For example, when transferring all settings the tool is transferring data in this order:
d. CMD_1 elements (if configured)
If CMD_1 elements are configured, it is recommended to send them at the beginning of the setting procedure as for some firmware versions, the setting tool sends them in wrong order – first trying to configure elements using CMD_1 and then to add CMD_1 itself to configuration. This would fail as element should be active
For example, when transferring all settings the tool is transferring data in this order:
You can have the protection functions configured also after step presented in point 3.a below - with 'tick' in the box for setting file in the 'Send to P139-660' window.
After this step device should have all control and protection functions configured and ready.
Make sure that IEC61850 is configured and enabled:
056.059 IEC Function group IEC With
104.000 IEC General enable USER Yes
Use context menu on the ‘Device’ branch:
And select the .mcl file for transfer: 
As mentioned previously, it is possible to send setting file in this window, just put 'tick' for valid setting name.
b. Serial communication (IEC 60870-5-103 / DNP3.0 / MODBUS)
Go to the COMM1 function group and send all parameters one-by one:
This is required as some of the parameters on this list has got attribute "Can only be sent individually":
Thus sending such parameter in group wouldn't work.
For example if user selects 'COMM1' for sending, the parameter mentioned above wouldn't be transferred.
It is a good habit to verify settings as the very last step of configuration procedure.
Select the second file and compare:
Then browse through all identified discrepancies and correct if necessary.
That’s all. Device is configured and ready for commissioning.
List of the required files:
- Setting file: .x3v
- IEC61850 configuration file: .mcl (if required)
- Customized bay type: .hex (if required)
It is recommended to start operation with device having default setting. Part of the configuration process is to recall bay type definition. This process fails if device would have assigned some I/O elements required by selected bay type. For example bay type = 2 needs UA01 (which is the U601 for 40TE case and U1201 for 84TE case):
If U901 (U1201) input is already assigned to any protection signal, the bay type setting would be rejected.
The rejection of the bay type assignment can be result of several configuration elements being present, thus instead of individual identification of all locking parameters it is recommended to start the setting procedure either with clean device – just after unpacking from factory package or to make it empty by means of cold restart.
Whole configuration process can be split into several parts, as follows:
1. Control part
a. If customized bay type requiredUpload .hex file to the device - please follow procedure from the document "TQ_PAST-2014-BW-03-c (ES1S for BTC download for P139[P439].65x)"
b. Type of bay
Open setting file and send the bay type number:
c. SIG_1 elements (if configured)
For example, when transferring all settings the tool is transferring data in this order:
152.145 INP Fct assign U 901 SIG_1 Signal S001 EXT
226.007 SIG_1 Signal S001 config. Yes
The first entry could be refused by the device as S001 is not active at this line.226.007 SIG_1 Signal S001 config. Yes
d. CMD_1 elements (if configured)
If CMD_1 elements are configured, it is recommended to send them at the beginning of the setting procedure as for some firmware versions, the setting tool sends them in wrong order – first trying to configure elements using CMD_1 and then to add CMD_1 itself to configuration. This would fail as element should be active
For example, when transferring all settings the tool is transferring data in this order:
150.193 OUTP Fct assign K 901 CMD_1 Command C001
200.004 CMD_1 Command C001 config. Yes
The first entry could be refused by the device as C001 is not active at this line.200.004 CMD_1 Command C001 config. Yes
2. Protection part
Just transfer all settings
Just transfer all settings
After this step device should have all control and protection functions configured and ready.
3. Communication part
a. IEC61850Make sure that IEC61850 is configured and enabled:
056.059 IEC Function group IEC With
104.000 IEC General enable USER Yes
Use context menu on the ‘Device’ branch:
As mentioned previously, it is possible to send setting file in this window, just put 'tick' for valid setting name.
b. Serial communication (IEC 60870-5-103 / DNP3.0 / MODBUS)
Go to the COMM1 function group and send all parameters one-by one:
This is required as some of the parameters on this list has got attribute "Can only be sent individually":
For example if user selects 'COMM1' for sending, the parameter mentioned above wouldn't be transferred.
4. Verification
It is a good habit to verify settings as the very last step of configuration procedure.
- Extract all settings
- Compare newly extracted file with the one used for configuration
Then browse through all identified discrepancies and correct if necessary.
That’s all. Device is configured and ready for commissioning.
Released for:Schneider Electric USA
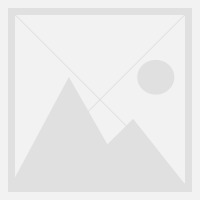
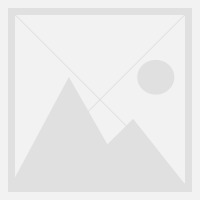
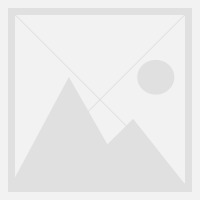
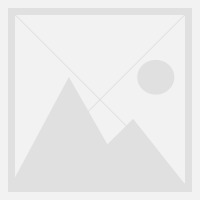
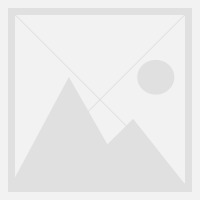
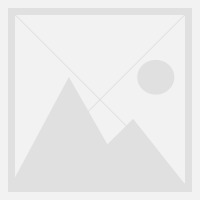
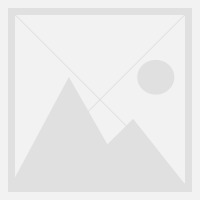
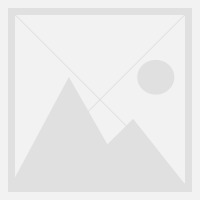
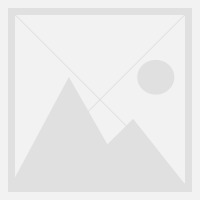
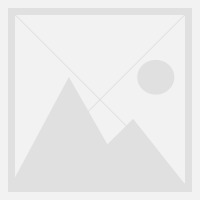