You are currently viewing the content available in Vietnam. If you are looking for information for another region, please select the correct country from the top-left dropdown in the page and 'Navigate to Browse FAQs' in the Support menu.
Issue:
ATV61 and ATV71 function of the process overload parameters
Product Line:
Altivar 61 and Altivar 71 series drives.
Environment:
All models, All serial numbers.
Cause:
Clarification of function is needed.
Resolution:
The Process overload function of the ATV61,ATV71 series drives (tol, loc, srb, odl parameters) is designed to trigger an overload fault at a point that is configurable by the user and not tied to the capabilities of the motor.
Parameter LOC sets the current at which the fault will be triggered. This can be set to a value between 70% and 150% of NCR parameter (Ncr parameter should be set to the motor Full Load Amps). TOL sets the amount of time the motor current needs to be above LOC value before the fault will be triggered and ODL parameter sets the behavior of the drive when this fault occurs. Srb parameter is set to trigger this fault when the motor speed falls below the reference frequency by a certain amount.
As an example:
We have a 75HP motor with a full load amp rating of 100 amps. It is powering an augur and we know that when the motor is running at full speed and the augur is fully loaded, the motor should only be pulling 80 amps (motor is oversized for the load). The normal motor overload will not be triggered until the motor is pulling more than the FLA rating of 100 amps, but we know our process is overloaded if the motor pulls more than 80 amps.
We would set parameter LOC to 80% (80% of 100 FLA = 80 amps) and we would also set TOL to 2 seconds. ODL parameter would be set to YES.
In this situation, if our motor current rises above 80 amps and stays there for more than 2 seconds, the process overload fault will be triggered and shut the drive down in a freewheel stop mode.
The SRB parameter is designed to stop the drive is the motor speed falls too far below the speed reference (motor jammed/stalled or load is slipping). SRB is set to a numerical value in Hz. If we have SRB set to 1.0 and our frequency reference at 30.0 Hz., the fault will be triggered if the actual motor speed falls below 29.0 Hz, regardless of the motor current.
For more information, please refer to page 212 of the ATV61 programming manual, document number 1760649_08.
ATV61 and ATV71 function of the process overload parameters
Product Line:
Altivar 61 and Altivar 71 series drives.
Environment:
All models, All serial numbers.
Cause:
Clarification of function is needed.
Resolution:
The Process overload function of the ATV61,ATV71 series drives (tol, loc, srb, odl parameters) is designed to trigger an overload fault at a point that is configurable by the user and not tied to the capabilities of the motor.
Parameter LOC sets the current at which the fault will be triggered. This can be set to a value between 70% and 150% of NCR parameter (Ncr parameter should be set to the motor Full Load Amps). TOL sets the amount of time the motor current needs to be above LOC value before the fault will be triggered and ODL parameter sets the behavior of the drive when this fault occurs. Srb parameter is set to trigger this fault when the motor speed falls below the reference frequency by a certain amount.
As an example:
We have a 75HP motor with a full load amp rating of 100 amps. It is powering an augur and we know that when the motor is running at full speed and the augur is fully loaded, the motor should only be pulling 80 amps (motor is oversized for the load). The normal motor overload will not be triggered until the motor is pulling more than the FLA rating of 100 amps, but we know our process is overloaded if the motor pulls more than 80 amps.
We would set parameter LOC to 80% (80% of 100 FLA = 80 amps) and we would also set TOL to 2 seconds. ODL parameter would be set to YES.
In this situation, if our motor current rises above 80 amps and stays there for more than 2 seconds, the process overload fault will be triggered and shut the drive down in a freewheel stop mode.
The SRB parameter is designed to stop the drive is the motor speed falls too far below the speed reference (motor jammed/stalled or load is slipping). SRB is set to a numerical value in Hz. If we have SRB set to 1.0 and our frequency reference at 30.0 Hz., the fault will be triggered if the actual motor speed falls below 29.0 Hz, regardless of the motor current.
For more information, please refer to page 212 of the ATV61 programming manual, document number 1760649_08.
Released for:Schneider Electric Vietnam
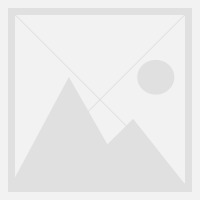
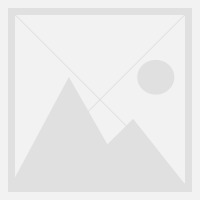
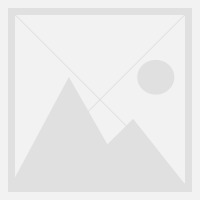
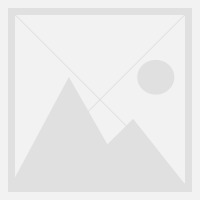